UNS N06600 AMS 5540 Strip
UNS N06600 AMS 5540 Strip Manufacturer
Uses of Inconel 600
As per UNS N06600 AMS 5540 Strip Manufacturer, Inconel 600 is used widely in the chemical industry, thanks to its strength and high corrosion resistance. Typical uses in this industry include heaters, stills, bubble towers, and processing condensers for fatty acids as well as tube, tube sheets, and flaking trays for producing sodium sulfide and for equipment handling abietic acid in producing pulp and paper goods. When heated, Inconel alloys form a thick yet stable oxide layer, which protects surfaces from increased attack.
Alloy 600 is also used in many applications in the heat-treating industry. The alloy’s strength and corrosion resistance at high temperatures make it ideal for furnace components, including mufflers, retorts, roller hearths, and heat-treating baskets and trays. Plus, Inconel 600 is used in aeronautics for engine and airframe components that need to withstand high temperatures like lockwire, turbine seals, and exhaust liners.
Alloy 600 is standard construction material in building nuclear reactors. It provides excellent corrosion resistance by high purity water, with no indication of chloride-ion stress-corrosion cracking in reactor water systems. Inconel 600 is produced to exacting specifications for nuclear applications and is referred to as Inconel 600T.
Machining and Working Instructions for Inconel Alloy 600
Alloy 600 is machinable into complex shapes, like pipe fittings, flanges, and valve parts. The main machining/cutting methods are drilling, boring, turning, grinding, and milling. This alloy is best machined using heavy-duty equipment and cutting tools large enough to withstand the loads and heat generated by the process. Tools must be sharp and have the correct geometry. The alloy is slightly more machinable than Type 304 stainless steel but slightly less machinable than type 303 free-machining stainless steel.
General machining characteristics of Inconel 600 include
- Large cutting forces and high cutting temperature, usually 1.5~2 times than carbon steel.
- The serious wear of cutting tools results in a very short service life.
- Serious work hardening during the machining.
- Very difficult to dispose of the chips during the machining process.
Several factors impact the alloy’s behavior during heating. These factors include the amount of cold work, grain size, chemical composition, and material dimensions. As a result, times and temperatures for heat treatment are generally experimentally determined. This alloy needs to be cleaned before it is heated in a sulfur-free atmosphere. Furnace atmosphere for forging and open annealing need to be slightly reducing to stop excessive oxidation. Inconel 600 can be bright-heated in a vacuum or dry hydrogen. Pickling is required for a bright surface.
Chemical Properties of Inconel 600
Element | Percent |
Nickel (plus Cobalt) (Min) | 72 |
Chromium | 14-17 |
Iron | 6-10 |
Carbon (Max) | .15 |
Manganese (Max) | 1 |
Sulfur (Max) | .015 |
Silicon (Max) | .5 |
Copper (Max) | .5 |
Alloy 600 Physical Properties (Annealed)
Property | Value |
Tensile Strength | 80.0 ksi |
Yield Strength at 0.2% Offset | 35.0 ksi |
Elongation in 4D | 30% |
Additional Properties of Inconel 600
A broad range of strengths and hardness is obtainable with Inconel 600, depending on form and condition UNS N06600 AMS 5540 Strip Manufacturer produce it . Alloy 600 exhibits moderate yield strengths of 25,000 to 50,00 psi (172 to 345 MPa) in the annealed condition. Yield strengths in that range, combined with elongations of 55% to 35%, make Alloy 600 easy to fabricate. Inconel 600 features good impact strength at room temperatures and tough-to-brittle with decreasing temperatures.
Inconel 600 is readably fabricated by hot or cold working and joinable by standard weld, brazing, and soldering processes. While cold work can strengthen and harden the alloy, manufacturers can obtain a wide range of mechanical properties in finished parts by combining cold work and heat treatments.
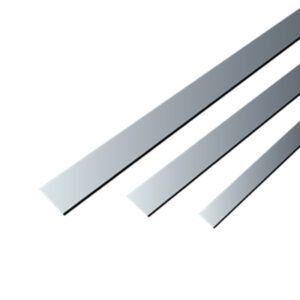
Attribute | Value |
AMS Number | AMS 5540 |
Alloy | Inconel 600 |
Type | Nickel |
UNS | N06600 |
Cross Reference Spec | – |
Misc./Shape | Inconel-600-strip |
Why Choose Us :
- As we are UNS N06600 AMS 5540 Strip Manufacturer ,You can get the perfect material according to your requirement at the least possible price from us .
- We also offer door to door delivery prices. We suggest you to do deal for shipping which will be quite economical.
- The materials we provide are completely verifiable, right from raw material test certificate to the final dimensional statement.(Reports will show on requirement)
- guarantee to give a response within 24hours(usually in the same hour)
- You can get stock alternatives, mill deliveries with minimizing manufacturing time.
- We are fully dedicated to our customers. If it will not possible to meet your requirements after examining all options, we will not mislead you by making false promises which will create good customer relations.
People Also Searched for
Stainless Steel ASTM A TP 304 Flanges Manufacturer, Stainless Steel ASTM A TP 304L Flanges Manufacturer, Stainless Steel ASTM A TP 304H Flanges Manufacturer, Duplex Steel ASTM 815 Flanges Manufacturer, Duplex Steel UNS S31803 Flanges Manufacturer, Duplex Steel S32750 Flanges Manufacturer, Duplex Steel S32760 Flanges Manufacturer, Duplex Steel S32205 Flanges Manufacturer, Nickel UNS N02200 Flanges Manufacturer, Nickel UNS N02201 Flanges Manufacturer, Alloy 20 Flanges Manufacturer, ASTM A 403 WP TP 304 Butt Weld Fittings Manufacturer, ASTM A 403 WP TP 304L Butt Weld Fittings Manufacturer, ASTM A 403 WP TP 304H Butt Weld Fittings Manufacturer, ASTM A 403 WP TP 316 Butt Weld Fittings Manufacturer, ASTM A 403 WP TP 316L Butt Weld Fittings Manufacturer, ASTM A 403 WP TP 316H Butt Weld Fittings Manufacturer, ASTM A 403 WP TP 316Ti Butt Weld Fittings Manufacturer, ASTM A 403 WP TP 309 Butt Weld Fittings Manufacturer, ASTM A 403 WP TP 904L Butt Weld Fittings Manufacturer, ASTM A 815- UNS S31803 Butt Weld Fittings Manufacturer, ASTM A 815- UNS S32750 Butt Weld Fittings Manufacturer, ASTM A 815- UNS S32760 Butt Weld Fittings Manufacturer, ASTM A 815- UNS S32205 Butt Weld Fittings Manufacturer, ASTM A 234 WPB – WP5 Butt Weld Fittings Manufacturer, ASTM A 234 WPB – WP9 Butt Weld Fittings Manufacturer, ASTM A 234 WPB – WP12 Butt Weld Fittings Manufacturer, ASTM A 234 WPB – WP22 Butt Weld Fittings Manufacturer, ASTM A 234 WPB – WP91 Butt Weld Fittings Manufacturer, ASTM A234 WPB Butt Weld Fittings Manufacturer, A420 WPL3 Butt Weld Fittings Manufacturer, A420 WPL6 Butt Weld Fittings Manufacturer, MSS-SP-75 WPHY 42 Butt Weld Fittings Manufacturer, MSS-SP-75 WPHY 46 Butt Weld Fittings Manufacturer, MSS-SP-75 WPHY 52 Butt Weld Fittings Manufacturer, C71640 Butt Weld Fittings Manufacturer, UNS N02200 Butt Weld Fittings Manufacturer, UNS N02201 Butt Weld Fittings Manufacturer, UNS N04400 Butt Weld Fittings Manufacturer, UNS N05500 Butt Weld Fittings Manufacturer, Alloy 20 Butt Weld Fittings Manufacturer, UNS N06600 Butt Weld Fittings Manufacturer, UNS N06601 Butt Weld Fittings Manufacturer, UNS N06625 Butt Weld Fittings Manufacturer, UNS N08800 Butt Weld Fittings Manufacturer, UNS N08810 Butt Weld Fittings Manufacturer, UNS N10276 Butt Weld Fittings Manufacturer, UNS N06022 Butt Weld Fittings Manufacturer, ASTM A 249 Stainless Steel Welded Manufacturer, ASTM A 268 Stainless Steel Welded Manufacturer, ASTM A 270 Stainless Steel Welded Manufacturer, ASTM A 554 Stainless Steel Welded Manufacturer, ASTM A 1016 Stainless Steel Welded Manufacturer. |
We Supply ASTM A234 WPB Butt weld Fittings in Andhra Pradesh, Arunachal Pradesh, Assam, Bihar, Chhattisgarh, Goa, Gujarat, Haryana, Himachal Pradesh, Jammu and Kashmir, Jharkhand, Karnataka, Kerala, Madhya Pradesh, Maharashtra, Manipur, Meghalaya, Mizoram, Nagaland, Odisha, Punjab, Rajasthan, Sikkim, Tamil Nadu, Telangana, Tripura, Uttar Pradesh, Uttarakhand, West Bengal, Mumbai, Navi Mumbai, Pune, Nashik, Nagpur, Solapur, Kolhapur, Ambernath, Ahmednagar, Latur, Ahmadabad, Surat, Rajkot, Vadodara, Panaji, Madgaon, Chennai, Kolkata, Hyderabad, Bengaluru, Delhi, New Delhi, Ludhiana, Chandigarh, Raipur, Bhopal, Jamshedpur, Vishakhapatnam, Cochin, Ghaziabad, Noida, Gurugram, Bhillai, Durgapur, Vijaywada, Kanpur etc. |