UNS N06625 AMS 5599 Sheet Nickel Alloy
UNS N06625 AMS 5599 Sheet Nickel Alloy Manufacturer
Description
Alloy 625 is a nonmagnetic , corrosion – and oxidation-resistant, nickel-based alloy. Its outstanding strength and toughness in the temperature range cryogenic to 2000°F (1093°C) are derived primarily from the solid solution effects of the refractory metals, columbium and molybdenum, in a nickel-chromium matrix. The alloy has excellent fatigue strength and stress-corrosion cracking resistance to chloride ions. Some typical applications for alloy 625 have included heat shields, furnace hardware, gas turbine engine ducting, combustion liners and spray bars, chemical plant hardware, and special seawater applications.
Corrosion Resistance
Alloy 625 has withstood many corrosive environments. In alkaline, salt water, fresh water, neutral salts, and in the air, almost no attack occurs. The nickel and chromium provide resistance to oxidizing environments. Nickel and molybdenum provide for resistance to nonoxidizing atmospheres. Pitting and crevice corrosion are prevented by molybdenum. Niobium stabilizes the alloy against sensitization during welding. Chloride stress-corrosion cracking resistance is excellent. The alloy resists scaling and oxidation at high temperatures.
Pickling
Sodium hydride baths are necessary to descale this alloy. After the sodium hydride treatment, the material should be immersed in a sulfuric acid bath 165°F (74°C) for approximately 3 minutes. A 25-minute immersion in a nitric-hydrofluoric bath 145°F (63°C) is then necessary. Rinse. Sulfuric solution: 16% by weight, H2SO4. Nitric solution: 8% HNO3 by weight and 3% HF by weight. Acid etching for macro-inspection-expose material electrolytically to a 3-to-1 HCl to HNO3 solution, saturated with CuCl2 at a current density of 0.645 amp/in² (25.4 A/m)
Fabrication
Annealing takes place between 1697℉ (925℃) and 1904℉ (1040℃), while a complete stress relief is achieved at 1598℉ (870℃). The effects of 1-hour annealing at room temperature to the hardness are optimal at 1697℉ (925℃), while significant adverse effects start to take place when going beyond 1900℉ (1038℃).
The optimal annealing point in relation to the tensile and yield strength of the Incoloy 625 is at 1301℉ (705℃), while significant losses start to become evident beyond 1508℉ (820℃).
Heat Treatment
Alloy 625 has three basic heat treatments:
- High Solution Anneal – 2000/2200°F (1093/1204°C), air quench or faster.
- Low Solution Anneal – 1700/1900°F (927/1038°C), air quench or faster.
- Stress Relieve – 1650°F (899°C), air quench.
The time at the above temperatures depends on volume and section thickness. Strip, for example, would require shorter times than large sections. Temperatures for treatments No. 1 and 2 are generally held for 1/2 to 1 hour, 1 to 4 hours for treatment No. 3.
Treatment No. 1 is not commonly used for applications below 1500°F (816°C). It is generally used above 1500°F and where resistance to creep is important. The high solution anneal is also used to develop the maximum softness for mild processing operations such as cold rolling or drawing.
Treatment No. 2 is the used treatment and develops an optimum combination of tensile and rupture properties from ambient temperatures to 1900°F (1038°C). Ductility and toughness at cryogenic temperatures are also very good.
Treatment No. 3 is recommended for application below 1200°F (649°C) when maximum fatigue, hardness, tensile and yield strength properties are desired. Ductility and toughness at cryogenic temperatures are excellent. When a fine grain size is desired for fatigue, tensile and yield strengths up to 1500°F (816°C), treatment No. 3 is sometimes used.
Workability
- Hot Working
Hot working may done at 2100°F (1149°C) maximum furnace temperature. Care should be exercised to avoid frictional heat build-up which can result in overheating, exceeding 2100°F (1149°C). Alloy 625 becomes very stiff at temperatures below 1850°F (1010°C). Work pieces that fall below this temperature should be reheated. Uniform reductions are recommended to avoid the formation of a duplex grain structure. Approximately 15/20% reduction is recommended for finishing.
- Cold Forming
Alloy 625 can be cold formed by standards methods. When the material becomes too stiff from cold working, ductility can be restored by process anneal.
- Machineability
Low cutting speeds, rigid tools and work piece, heavy equipment, ample coolant and positive feeds are general recommendations.
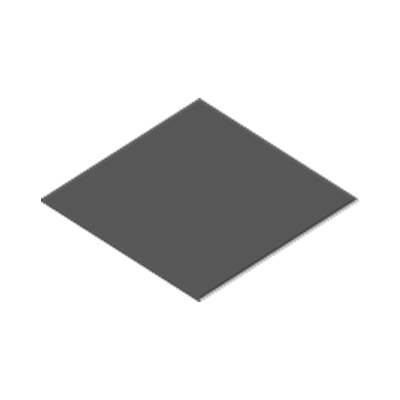
High-Speed Cutting Tools for Lathe Turning Operations
Angle | Roughing | Finishing |
Back rake Positive side rake End clearance End cutting edge Side cutting edge | 0° 6° | 8° 14-18° 8° 25° Up to 45° |
Cutting Speeds for High-Speed Steels
Operation | Speed | Feed | ||
sfpm | m/s | ipr | mm/rev | |
Turning Drilling (.500″/12.70mm) Tapping Milling Reaming | 12-20 10-12 5-10 10-20 8-10 | 0.06/.010 0.05/0.06 0.03/0.05 0.05/0.10 0.04/0.05 | 0.010 0.006/0.010 — — — | 0.25 0.15/0.25 — — — |
Carbide tools should have smaller angles than high-speed tools and operating speeds can be higher. A sulfur-based cutting fluid is recommended. Thoroughly clean work piece after machining to prevent surface contamination during subsequent heat treating. Chlorine additives would be an alternative.
Weldability
Welding can be accomplished by the gas-shielded processes using a tungsten electrode or a consumable electrode. Postweld heat treatment of the weld are not necessary to maintain corrosion resistance. Heavy restrained sections can be welded and the weld’s mechanical properties follow the same trends as base metal properties. Standard practices such as clean surfaces, good joint alignment, U-joints for thicker sections, etc., should be followed.
Why Choose Us :
- You can get the perfect material according to your requirement at the least possible price.
- We also offer door to door delivery prices. We suggest you to do deal for shipping which will be quite economical.
- The materials we provide are completely verifiable, right from raw material test certificate to the final dimensional statement.(Reports will show on requirement)
- guarantee to give a response within 24hours(usually in the same hour)
- You can get stock alternatives, mill deliveries with minimizing manufacturing time.
- We are fully dedicated to our customers. If it will not possible to meet your requirements after examining all options, we will not mislead you by making false promises which will create good customer relations.
People Also Searched for
Stainless Steel ASTM A TP 304 Flanges Manufacturer, Stainless Steel ASTM A TP 304L Flanges Manufacturer, Stainless Steel ASTM A TP 304H Flanges Manufacturer, Duplex Steel ASTM 815 Flanges Manufacturer, Duplex Steel UNS S31803 Flanges Manufacturer, Duplex Steel S32750 Flanges Manufacturer, Duplex Steel S32760 Flanges Manufacturer, Duplex Steel S32205 Flanges Manufacturer, Nickel UNS N02200 Flanges Manufacturer, Nickel UNS N02201 Flanges Manufacturer, Alloy 20 Flanges Manufacturer, ASTM A 403 WP TP 304 Butt Weld Fittings Manufacturer, ASTM A 403 WP TP 304L Butt Weld Fittings Manufacturer, ASTM A 403 WP TP 304H Butt Weld Fittings Manufacturer, ASTM A 403 WP TP 316 Butt Weld Fittings Manufacturer, ASTM A 403 WP TP 316L Butt Weld Fittings Manufacturer, ASTM A 403 WP TP 316H Butt Weld Fittings Manufacturer, ASTM A 403 WP TP 316Ti Butt Weld Fittings Manufacturer, ASTM A 403 WP TP 309 Butt Weld Fittings Manufacturer, ASTM A 403 WP TP 904L Butt Weld Fittings Manufacturer, ASTM A 815- UNS S31803 Butt Weld Fittings Manufacturer, ASTM A 815- UNS S32750 Butt Weld Fittings Manufacturer, ASTM A 815- UNS S32760 Butt Weld Fittings Manufacturer, ASTM A 815- UNS S32205 Butt Weld Fittings Manufacturer, ASTM A 234 WPB – WP5 Butt Weld Fittings Manufacturer, ASTM A 234 WPB – WP9 Butt Weld Fittings Manufacturer, ASTM A 234 WPB – WP12 Butt Weld Fittings Manufacturer, ASTM A 234 WPB – WP22 Butt Weld Fittings Manufacturer, ASTM A 234 WPB – WP91 Butt Weld Fittings Manufacturer, ASTM A234 WPB Butt Weld Fittings Manufacturer, A420 WPL3 Butt Weld Fittings Manufacturer, A420 WPL6 Butt Weld Fittings Manufacturer, MSS-SP-75 WPHY 42 Butt Weld Fittings Manufacturer, MSS-SP-75 WPHY 46 Butt Weld Fittings Manufacturer, MSS-SP-75 WPHY 52 Butt Weld Fittings Manufacturer, C71640 Butt Weld Fittings Manufacturer, UNS N02200 Butt Weld Fittings Manufacturer, UNS N02201 Butt Weld Fittings Manufacturer, UNS N04400 Butt Weld Fittings Manufacturer, UNS N05500 Butt Weld Fittings Manufacturer, Alloy 20 Butt Weld Fittings Manufacturer, UNS N06600 Butt Weld Fittings Manufacturer, UNS N06601 Butt Weld Fittings Manufacturer, UNS N06625 Butt Weld Fittings Manufacturer, UNS N08800 Butt Weld Fittings Manufacturer, UNS N08810 Butt Weld Fittings Manufacturer, UNS N10276 Butt Weld Fittings Manufacturer, UNS N06022 Butt Weld Fittings Manufacturer, ASTM A 249 Stainless Steel Welded Manufacturer, ASTM A 268 Stainless Steel Welded Manufacturer, ASTM A 270 Stainless Steel Welded Manufacturer, ASTM A 554 Stainless Steel Welded Manufacturer, ASTM A 1016 Stainless Steel Welded Manufacturer. |
We Supply ASTM A234 WPB Butt weld Fittings in Andhra Pradesh, Arunachal Pradesh, Assam, Bihar, Chhattisgarh, Goa, Gujarat, Haryana, Himachal Pradesh, Jammu and Kashmir, Jharkhand, Karnataka, Kerala, Madhya Pradesh, Maharashtra, Manipur, Meghalaya, Mizoram, Nagaland, Odisha, Punjab, Rajasthan, Sikkim, Tamil Nadu, Telangana, Tripura, Uttar Pradesh, Uttarakhand, West Bengal, Mumbai, Navi Mumbai, Pune, Nashik, Nagpur, Solapur, Kolhapur, Ambernath, Ahmednagar, Latur, Ahmadabad, Surat, Rajkot, Vadodara, Panaji, Madgaon, Chennai, Kolkata, Hyderabad, Bengaluru, Delhi, New Delhi, Ludhiana, Chandigarh, Raipur, Bhopal, Jamshedpur, Vishakhapatnam, Cochin, Ghaziabad, Noida, Gurugram, Bhillai, Durgapur, Vijaywada, Kanpur etc. |